Cobalt crisis a nightmare for Electric Cars
Batteries are the main source of power in our daily lives, our phones as well as laptops use battery to faction.
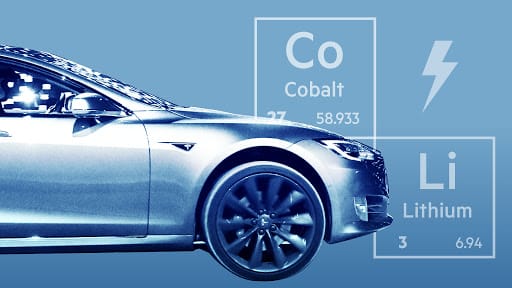
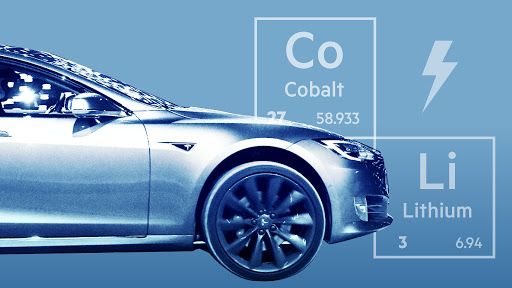
Batteries are the main source of power in our daily lives, our phones as well as laptops use battery to faction. In order for electric vehicles to replace ICE there is a need to have many battery companies that are willing to manufacture many batteries in order to accommodate the rising demand of the electric cars. With an estimation of 12 million EVs expected in 2025 this translates for a more gigafactories that can manufacture more batteries.
Electric cars are the future, and so are the batteries that power them. Yet, these batteries are dependent on cobalt, which has linked the electric vehicle industry to one of the most unstable countries in the world, and to practices like child labor. This, along with the metal’s high cost, has started a race to replace cobalt.
The electric car service is predicted to top four million cars globally in 2020, rising to 12 million in 2025. In Europe more than a half million electric cars have been sold this is an increase compared to 319,000 cars that were sold in 2019. And for this reason not only do we need gigafactories to build electric batteries but what is needed mostly is the raw materials for manufacturing the batteries, Lithium and cobalt that is currently scarce globally.
Jaguar and Land Rover are among the companies that have stopped their production due to battery shortages. "Currently EV uptake is arguably being constrained more by lack of manufacturing capacity than anything else," says Paul Anderson, co-director of the Birmingham Centre for Strategic Elements and Critical Materials. "Lack of battery manufacturing capacity is a key part of this, which is why there is the rush to build gigafactories."
Gavin Harper, research fellow at the Faraday Institution, a battery research group, says gigafactories is a problem that can be easily tackled, in 2019 June there were about 91 factories that were producing lithium ion cells around the world, of which around half were already in production the previous year. “What isn’t so easily solved is the issue of getting enough raw materials out of the ground."It’s been predicted that as demand for electric vehicles surges, there could be constraints around the key strategic elements and critical materials needed for EV battery manufacture in the future,” says Harper.
Lithium and cobalt are critical components in batteries for electric cars. The rapid growth in the demand for rechargeable batteries has now driven up these raw material prices, and given rise to concerns about potential cobalt and lithium scarcities that could slow the roll-out of electric vehicles. The price of cobalt is expected to remain high due to limited supply and growing demand. The materials are not only the problem but there is an issue of geopolitical upheaval including trade wars, local protests and the raise of human rights and economical concerns, which is likely to cause under supply of the EVs.
At the moment there is enough supply of Lithium, but only segmented in Australia, Argentina and Chile , it provides 91 per cent of supply in 2017, says Harper – a slump in demand caused by a weak automotive market and a reduction in grants for buying such cars in China has slowed the pace of mining and processing plant construction.
Leyland says back in 2015, there were close to 15 such lithium mines. "Now you're closer to 30, 35," he says. Most of those are in Australia, which is now the world’s biggest producer of lithium with China its biggest customer; back in the 1990's, the US was the main lithium supplier to the world, but now it has just one major producer. But just because the lithium isn’t on your land doesn’t mean you can’t get at it. The US does still have small lithium deposits – in particular, around the Salton Sea in California – but deposits in Australia and South America are vast by comparison. But America, Leyland points out, owns two of the largest chemical companies.
Lithium-ion batteries in electric cars use either nickel cobalt aluminum or nickel manganese cobalt oxides for their ability to offer a long lifespan and high energy density therefore a determining factor in how far a single charge can power an electric car.
Battery cells rely on four main parts: a positive and negative electrode, a separator and a liquid electrolyte. The positive electrode, or cathode, is coated in a careful processed metal oxide slurry that in most cars includes lithium, cobalt, nickel and manganese. When the battery is discharged, lithium ions flow to the cathode generating a flow of electrons and electricity. When the battery is recharged they flow back to the anode, the negative electrode, which is normally made of graphite. Cobalt is essential for stopping the battery from overheating and the stability it brings to the battery materials also allows users to charge and discharge their car over many years. But it is also the most expensive of the metals used therefore hindering the ability of carmakers to lower the cost of electric cars to compete against their petrol counterparts.
EVs that go for short range will use lithium-ion phosphate batteries, which are cheaper and do not have same environmental problems like those will need cobalt. However, the disadvantage is that these batteries tend to have a lower energy density, reducing how far a car can drive without needing to charge.
Industry analysts such as Simon Moores at Benchmark Mineral Intelligence in London suggests the move is unlikely to be replicated outside China, saying it is driven more by a desire to reduce production costs in China than to phase out cobalt.
Child labour
Unlike lithium, the price of cobalt is expected to remain high due to limited supply and growing demand. Democratic Republic of Congo produces 60% of the world's supply of cobalt. The mineral is used to produce lithium-ion batteries used to power electric cars, laptops and Smartphone’s. However, the extraction process has been beset with concerns of illegal mining, human rights abuses and corruption.
There are 150,000 miners in Kolwezi, the regional capital in southern DRC that has become a major mining centre, according to Mark Dummett, a researcher on business and human rights at Amnesty International. Children working at the mines are easy to find within a five-minute drive of the city centre, he said.
But just as the silver like-gray metal has established itself as a critical element in the growth of the market in electric vehicles (EVs), cobalt has also become a source of serious ethical and economic concerns. The majority of the world’s cobalt production is concentrated in the Democratic Republic of Congo, where in many cases children work in hazardous conditions mining the metal.
Cobalt is important in electric cars because the cathodes in lithium-ion batteries typically used in EVs are made of metal oxides that contain a combination of cobalt and other elements. Cobalt helps the cathodes concentrate a lot of power in a confined space. Without the element’s energy density, batteries in EVs will not function well.
As the EV sector attempts to move from niche-market status to mainstream acceptance, cobalt demand is surging. For example California policymakers have pushed zero-emissions vehicles as essential to meet the state’s mandates to dramatically reduce greenhouse gas emissions.
Recycling batteries
Current recycling rates for cobalt are relatively low, while those for lithium are historically insignificant. To be able to recycle batteries to the scale that the growing electric vehicle market demands, the industry will need to solve some key challenges. First of all, today’s batteries aren’t designed for easy disassembly. Batteries aren’t all made in one standard way, making it difficult to automate taking them apart. A lot of the handwork need to be done by people who are skilled to avoid hurting themselves in the process of disassembling the batteries. Putting in mind these batteries can explode, in case of an explosion they emit noxious gases. And the types of sealants and adhesives that are used in batteries are extremely strong, making workers’ jobs harder.
Robots can be used to disassemble the batteries, but they need more advanced batteries in order to deliver good work. Easier disassembling could lead to extracting purer and, consequently, more valuable materials from the batteries that can then be sold or used to manufacture new batteries.
Also read: Cobalt crisis facing electric cars